S-5! VersaGard™
VersaGard is a metal roof bracket used for both PV installation and snow retention on exposed-fastened metal roofs.
FAQs
The key to frequency and spacing of attachment points for PV is to distribute loads to the metal standing seam panels in a manner that is consistent with the intended distribution of loads from the roof panels into the building structure.
NOTE: The following suggestions assume that determination has been made that the roof to which the S-5! clamps will be attached is structurally adequate. Any loads imposed on the S-5! clamps will be transferred to the panels. Panel seams must have sufficient flexural strength to carry these loads. Panels must also be adequately attached to the building structure, and the structure must be sufficient to carry these loads. The makers of S-5! clamps make no representations with respect to these variables. It is the responsibility of the user to verify this information or seek assistance from a qualified design professional, if necessary.
With very few exceptions, the attachment of a single S-5! clamp (even the “Mini”) to the seam will be stronger than a single point of attachment of the seam to the building structure. Hence the “weak link” is not the S-5! clamp, but the attachment clips that hold the metal panels to the building structure, or the beam strength of the roof panel seam, itself.
The most conservative approach to the spacing/frequency of PV attachment to the roof is to determine the spacing/frequency of the roof’s attachment to the building structure; then duplicate it at minimum.
Determining panel attachment spacing in one axis is very simple: Standing seam panels’ attachment will be made using concealed hold-down clips within the seam area of the panel. So, in that axis, the clip spacing is the same as the seam spacing. The location of the clips along the seam (in the other axis) can be determined by
a) consultation with the roof system manufacturer or installer,
b) checking from the underside or,
c) close examination from the topside along the seam. There will usually be a slight, but detectable, deformation of the seam at the clip location visible from the roof’s topside. Many standing seam roofing systems are installed on “pre-engineered steel” buildings. The attachment spacing in that industry is typically 5’-0” and is readily apparent by inspecting the structural purlins to which the panel clips are attached from the roof underside (interior of the building).
If the panel clips are spaced, for instance, 5′-0″ on center along the seam, then use the 5′-0″ dimension as a maximum spacing for the S-5! clamps. (S-5! clamps may also be spaced at closer centers, but not wider.) When modules are direct-attached (without racking) in the landscape orientation, this spacing dimension is dictated by the smallest dimension of the PV frame.
Using the roof panel clip spacing as a maximum spacing template for S-5! clamps is a sound practice, whether the PV modules are attached directly to S-5! clamps or brackets, or to a racking system, which is in turn attached to the S-5! attachments (and then panel seams).
To evenly distribute loads, it is also necessary that each seam be involved in the finished assembly. Thus, every time a seam is traversed, it should be attached. Such an attachment scheme should evenly distribute wind loads into the building structure through the panels and their attachment, as was intended in the original roof construction assembly.
Please note these are only suggestions. Wind dynamics are complex, and S-5! advises review by a qualified licensed professional who understands wind effects and metal roof design and construction.
The S-5 PVKIT / S-5! standing seam clamp assembly is a UL2703 listed bonding device. While the listing covers carrying a ground path from PV panel to PV panel, the clamp to the roof panel material is not included in this certification.
On an individual basis, some independent racking companies have worked with certification labs to verify the clamp-to-roof connection and its reliability as a bonding path. For instance, IronRidge has found that S-5! clamps provide a reliable bond path between the clamps and the roofing panels beneath the array. This rating is included in their racking systems UL2703 listing.
IronRidge Flush Mount Installation
IronRidge Tilt Mount Installation
Grounding path as concerns module-level-power electronics (MLPE): If the microinverter does not have internal grounding, then it will need to be independently grounded when fixed to the roof. If the microinverter is fixed to the module frame, then it can be grounded via the module frame.
S-5! brackets feature integrated sealant reservoirs to prevent over-compression of the seal and to protect the sealant from UV degradation. No risky, field applied sealants are ever used. No need to source sealant materials. Instead, you get permanence, convenience, maintenance freedom, ease of installation, a complete assembly, and peace of mind.
No, it will deteriorate with exposure and can then do more harm than good.
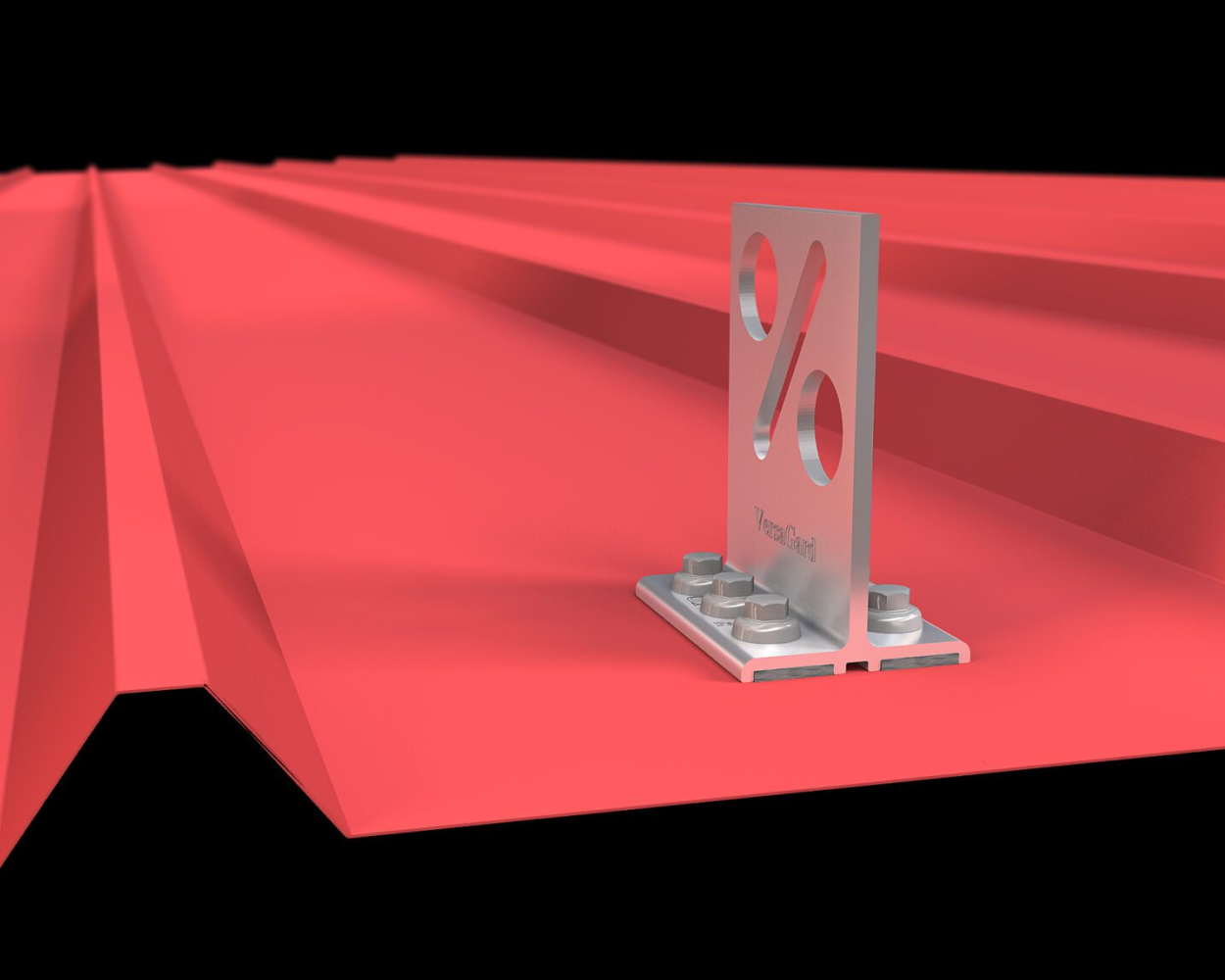